Numerical Optimum Design of Prosthetic Shank Made of Fiber Carbon Material and Cross Section Area
Keywords:
Prosthetic shank, Carbon fiber material, Lightweight and durability, Biomechanics, Human gait analysisAbstract
Certain individuals or animals may necessitate the fitting of a prosthetic limb above the knee or the implantation of an artificial hip joint due to amputation, which can arise from various factors such as congenital anomalies, chronic illnesses, or severe injuries that lead to the necrosis of leg tissues and damage to adjacent arteries. The healing process typically requires a duration of 2 to 3 months following the amputation, owing to the sensitivity of the residual limb.
Lower limb amputations are predominantly the result of accidents or medical conditions. In our research, we have identified PETG as a suitable material for the production of prosthetics. This material is particularly advantageous due to its affordability, unique mechanical properties, and favorable safety factor. It is lighter and more convenient compared to other high-pressure materials, which tend to be heavier. In this study, we concentrated on developing the optimal design for the lower limb (shank) prosthesis by examining various cross-sectional shapes using carbon fiber. We designed samples of this material and conducted tensile tests to ascertain its mechanical properties. Additionally, we utilized the Ansys program to model and analyze the Finite Element Method, comparing the different cross-sections. By applying two weights, we calculated the effects of the imposed forces in terms of deformation, stress, and safety factor. The results indicated that the circular and elliptical sections exhibited similar performance across all metrics, with only a negligible difference. Conversely, the hexagonal section demonstrated the least resistance to stress and experienced significant deformation compared to the other shapes, suggesting that circular or elliptical designs are preferable for prosthetic applications.
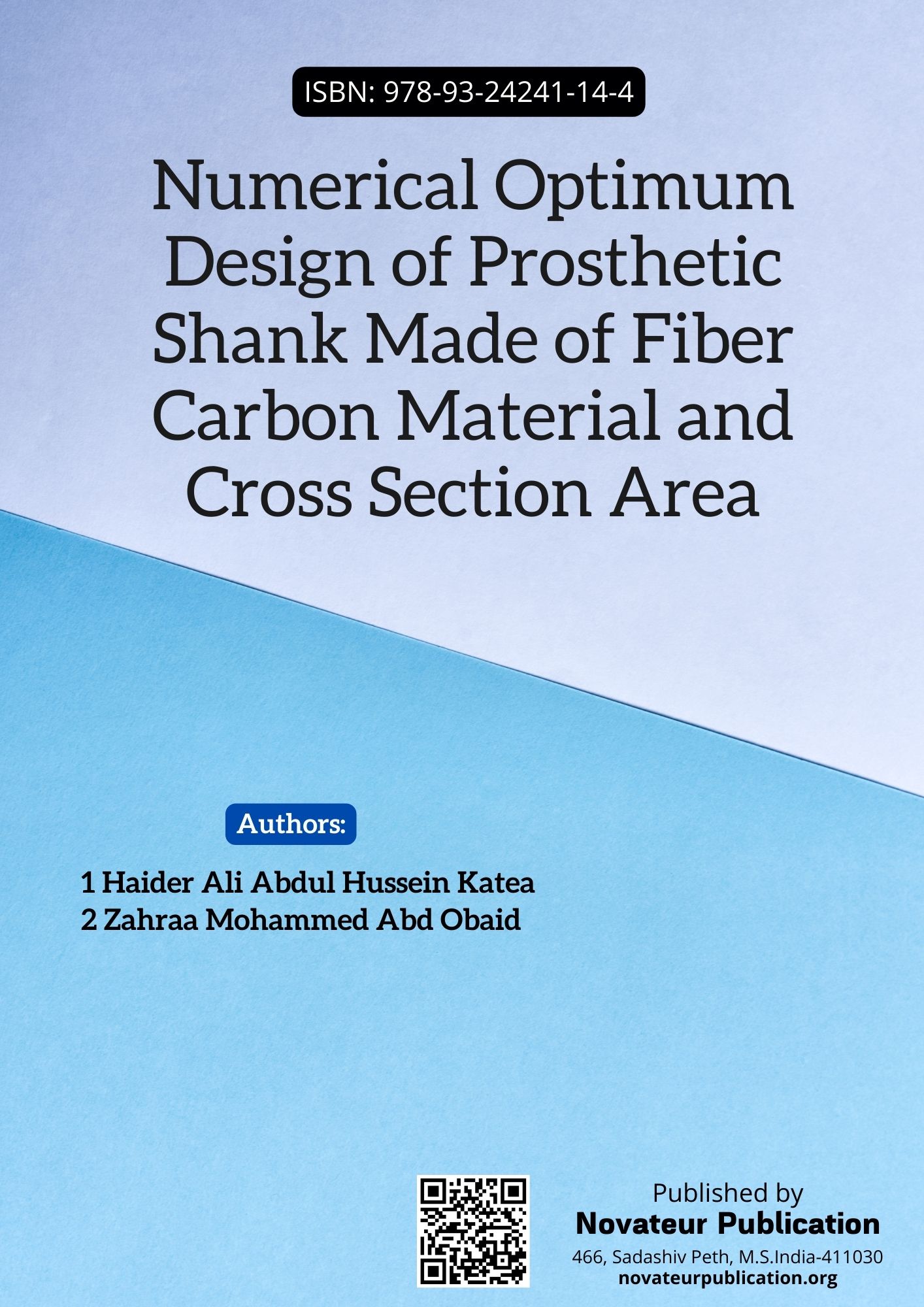
Downloads
Published
Issue
Section
License

This work is licensed under a Creative Commons Attribution-NonCommercial 4.0 International License.